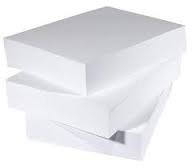
Paper is the often overlooked weak spot when clients report less than desired results from their copiers or printers. “We need a tech please, right away, the copier or printer isn’t working right.” Of course, a tech is dispatched because that’s what we do, but when I review the calls with the techs, it isn’t unheard of to find out that the client’s paper choice isn’t the best fit for the device. So, what sort of things are there to look out for?
Low quality paper is going to result in low quality results, no matter how wonderful the copier or printer. Buyers should consider what they are printing first to help determine what paper to use. For instance, are these simply basic office documents or is it a customer presentation that needs to be done?
Determine which weights the copier or printer can handle successfully. All machines have listed limitations and specifications. And, where something outside of those may work, you won’t get the results you seek for long, if you don’t choose to work with paper that fits those specifications. Things to look for are the paper weight, the paper finish, the paper brightness, is it multi-purpose, recycled, inkjet, or laser, what is the paper made of (cotton, wood, recycled material, etc…) and what is the finish? Copiers and printers are made to work with media that falls within certain specifications.
Take a look at how you are storing your paper. Make sure it is in a climate controlled area. Summer time brings more jams as temperatures heat up and humidity increases. Paper reacts to the environment and copiers and printers react to the paper. Make sure you rotate your paper in the trays if it has been sitting a long time without use. Turn it over and around to help keep it flat.
Most copiers and printers allow you to choose the paper types you are using. Not just the sizes, but the weights and the types. When these settings are adjusted before a job, the machines adjust themselves to the paper input. They may warm or cool a little, apply more or less pressure to the rollers, put down more or less toner, or make other adjustments to ensure the best results. Make sure you understand and make the adjustments necessary before you proceed with your printing. Your jobs will come out better for it.
Finally, use the best paper you can for all situations. Sometimes the least expensive paper causes the most problems. Not all the time, but some of the time. Perhaps the paper kicks off a lot of dust which settles in the machine parts, or maybe it has a finish on it which prevents the ink or toner from adhering to the page. Many of the quality issues customers report on are caused by cheap paper.
The devil is in the details when it comes to getting the best results from your print devices. Paper is often the overlooked cause of issues.